Understanding the Impact of 3D Printing on Car Manufacturing
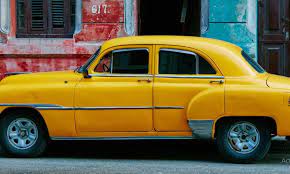
In the dynamic landscape of automotive manufacturing, traditional methods are making way for cutting-edge technologies. One such revolutionary advancement is the integration of 3D printing into the car manufacturing process. This blog explores the profound impact of 3D printing on the automotive industry, from enhancing design flexibility to optimising production efficiency. As we delve into the transformative innovations, it’s also essential to consider the lifecycle of vehicles. If you’re in Blacktown and seeking a streamlined solution for your old car, explore car removals in Blacktown for a convenient and efficient way to part with your vehicle, aligning with the progressive trends in automotive technology.
Unleashing Design Flexibility
The traditional constraints of manufacturing often limit design possibilities, but 3D printing is changing the game. This technology allows for intricate and complex designs that were previously challenging or impossible to achieve. Car manufacturers can now create components with optimised shapes, reducing weight without compromising structural integrity. The newfound design flexibility contributes to the development of sleeker, more aerodynamic vehicles.
Optimising Prototyping and Testing
One of the notable advantages of 3D printing in car manufacturing is its role in rapid prototyping. Traditional prototyping processes were time-consuming and expensive, but 3D printing enables the quick and cost-effective production of prototypes. Manufacturers can easily iterate and refine designs, accelerating the overall product development cycle. This efficiency extends to testing, where prototypes can be subjected to real-world conditions for more accurate assessments.
Customization and Personalization
Consumer preferences are increasingly leaning towards personalised products, and 3D printing aligns perfectly with this trend. Car manufacturers can offer customers a level of customization that goes beyond cosmetic features. From tailored interior components to unique exterior elements, 3D printing allows for the creation of bespoke automotive designs, providing customers with a truly individualised driving experience.
Enhancing Supply Chain Efficiency
Traditional manufacturing often involves complex supply chains and large inventories of spare parts. 3D printing introduces the concept of on-demand manufacturing, where components can be produced as needed. This not only reduces the need for extensive storage but also minimises waste, contributing to a more sustainable manufacturing process. The streamlined supply chain results in cost savings and a more environmentally friendly approach.
Material Innovation and Lightweighting
3D printing opens the door to a wide range of materials beyond traditional metals and plastics. Advanced materials, such as carbon fibre-reinforced polymers, can be utilised in 3D printing processes. This innovation allows for the creation of lightweight yet robust components, enhancing fuel efficiency and overall vehicle performance. The ability to experiment with materials contributes to ongoing efforts in the automotive industry to develop more sustainable and eco-friendly solutions.
Challenges and Future Prospects
While 3D printing holds immense promise, it is not without challenges. Scaling up production to meet the demands of mass manufacturing is a hurdle that the industry continues to address. Additionally, the need for standardised processes and quality control measures is crucial to ensuring the safety and reliability of 3D-printed automotive components. As technology advances and these challenges are addressed, the future prospects for 3D printing in car manufacturing are exceptionally bright.
Addressing Production Scalability
As the automotive industry steers towards the widespread adoption of 3D printing, addressing production scalability becomes a critical consideration. While 3D printing offers unparalleled flexibility and efficiency, seamlessly transitioning from prototyping to mass production is a challenge that manufacturers are actively tackling. Innovations in large-scale 3D printing technologies and the optimization of production workflows are underway to meet the demands of high-volume manufacturing.
Standardising Processes for Quality Assurance
Ensuring the consistent quality of 3D-printed automotive components is paramount for safety and reliability. The industry is actively working on standardising processes and implementing rigorous quality control measures to meet and exceed regulatory standards. This includes developing industry-wide guidelines for material selection, printing parameters, and post-processing techniques. As these standards evolve, they will provide a solid foundation for the integration of 3D printing into mainstream car manufacturing.
Revolutionising Spare Parts Production
The concept of on-demand manufacturing facilitated by 3D printing extends beyond the initial production phase. Car manufacturers are exploring the possibilities of producing spare parts on-demand, minimising the need for extensive warehouses and reducing the time required for repairs. This not only streamlines the supply chain but also enhances the overall efficiency of vehicle maintenance, potentially transforming the way we approach car repairs and part replacements.
Fostering Sustainability in Car Manufacturing
The environmental impact of traditional manufacturing processes has prompted the automotive industry to seek more sustainable alternatives. 3D printing aligns with sustainability goals by minimising material waste and enabling the use of eco-friendly materials. Additionally, the lightweight components produced through 3D printing contribute to fuel efficiency, further advancing the industry’s commitment to environmental responsibility. Embracing 3D printing is, therefore, a strategic move towards fostering sustainability within the automotive sector.
Collaboration and Knowledge Sharing
The journey towards integrating 3D printing into mainstream car manufacturing is characterised by collaboration and knowledge sharing. Industry players, research institutions, and technology pioneers are actively collaborating to share insights, best practices, and innovations. This collaborative spirit accelerates the learning curve, fosters innovation, and creates a collective momentum that propels the automotive industry towards a future where 3D printing is an integral part of the manufacturing landscape.
The Future Landscape of Car Manufacturing
As 3D printing continues to evolve, the future landscape of car manufacturing holds exciting possibilities. The convergence of design freedom, efficiency gains, and sustainability aligns with broader industry trends. The automotive sector stands on the precipice of a paradigm shift, where the manufacturing process becomes not just a means to an end but a dynamic and adaptive system that responds to evolving consumer demands and global challenges.
Conclusion
In conclusion, the influence of 3D printing on car manufacturing extends far beyond the initial stages of design and prototyping. It represents a transformative force that is reshaping the industry’s approach to production, supply chain management, and sustainability. While challenges exist, ongoing advancements, collaborative efforts, and a commitment to quality assurance are propelling the automotive sector towards a future where 3D printing is a mainstream and indispensable component of the manufacturing process. The road ahead is paved with opportunities for innovation, efficiency, and a more sustainable approach to crafting the vehicles that drive us into the future.